MANIFICA : Manufacturing and Innovation with Recycled Carbon Fibers
The global ambition of MANIFICA was to set up the recycling chain of carbon fibre composites “from aeronautic waste to innovative composite parts”
One of the first step of the project was to organize collection and sorting of carbon production waste in France. This was implemented directly at major aeronautical premises by our partner Paprec, a waste collection and plastic recycling specialist across Europe
Then, MANIFICA project used the I2M rCF patented realignment technology to produce rCF semi-products with highly aligned long recycled carbon fibres.
Thanks to this technology, recycled carbon fibres are turned into various semi-products that can be used to manufacture new rCF composite parts. VESO Concept participated actively to the definition this semi-products, in close cooperation with I2M, to obtain rCF tapes providing sufficiant strength and stiffness to manufacture semi-structural parts.
In this project, thanks to our expertise in the design of environmentally friendly composite materials, VESO Concept was in charge several key points of the project :
- Life Cycle Analysis of the whole value chain and the economic viability of the semi-products.
- Development of a composite material with rCF
- Manufacture two demonstrators with recycled carbon fibres from I2M
The Life Cycle Analysis showed very promising results of the use of Recycled Carbon Fibers
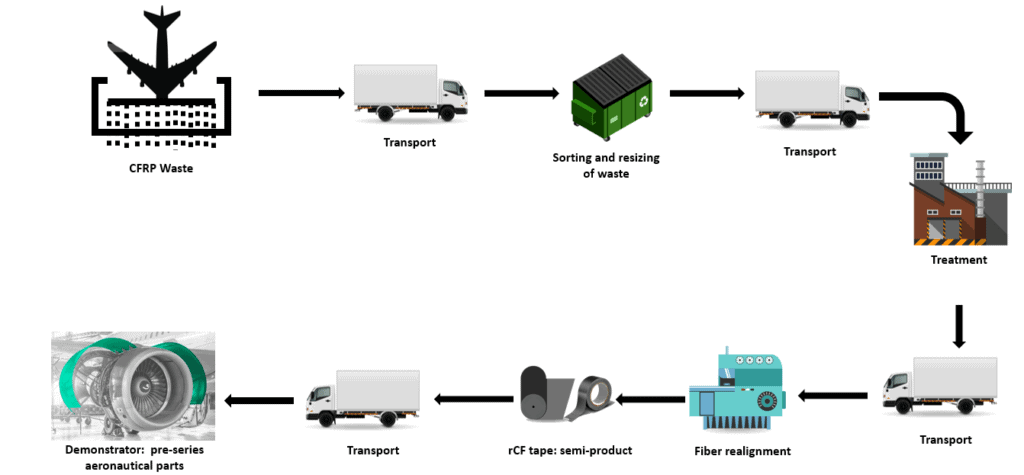
Fell free to discover details concerning the LCA analysis
VESO Concept work on the development of a new composite material made with recycled carbon fibres required many steps several matrices and processing trials. Finally we kept several processing methods, depending on the complexity of the final piece. For example, manufacturing with rCF prepregs and vacuum infusion process were retain.
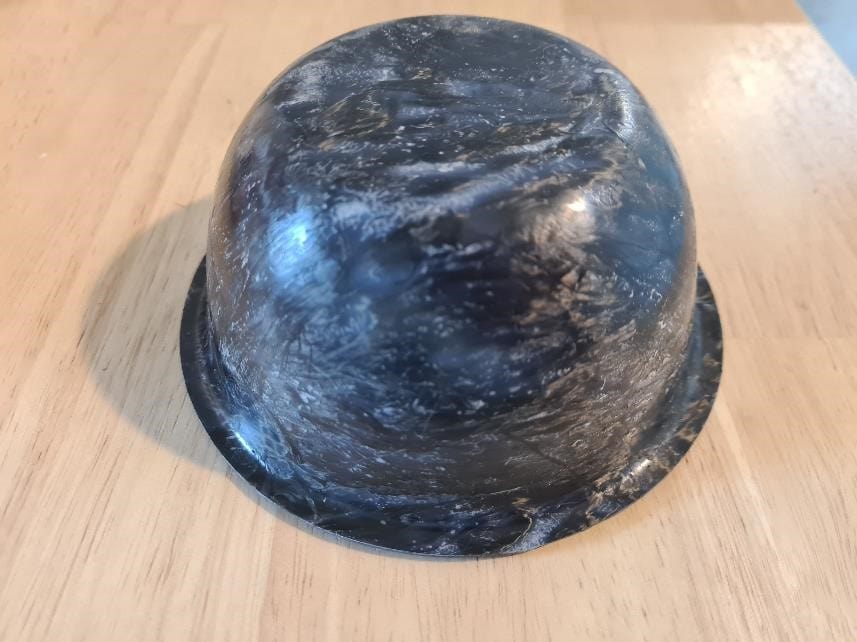
Regarding the manufacturing of demonstrators, VESO Concept was able to produce two parts of an airplane : a floor panel and a part of an AIOS
For the floor panel, we first manufactured the skins from homemade prepregs cured at low temperature. This gave us skins with sufficient flatness to glue both skins on each side of a Nomex honeycomb panel. To get a satisfactory result, several finishing passes were needed.
The AIOS has been manufactured by vacuum infusion technique, with a piling of 3 oriented plies of rCF. The piece was then unmolded and cutted out to get the final piece.
In both case, we had to adapt our manufacturing process to the piece due to rCF technical constraints , but the result is as high as our ambition, with significantly high fibre ratio (63% for the AIOS) and almost no porosity on the surface.
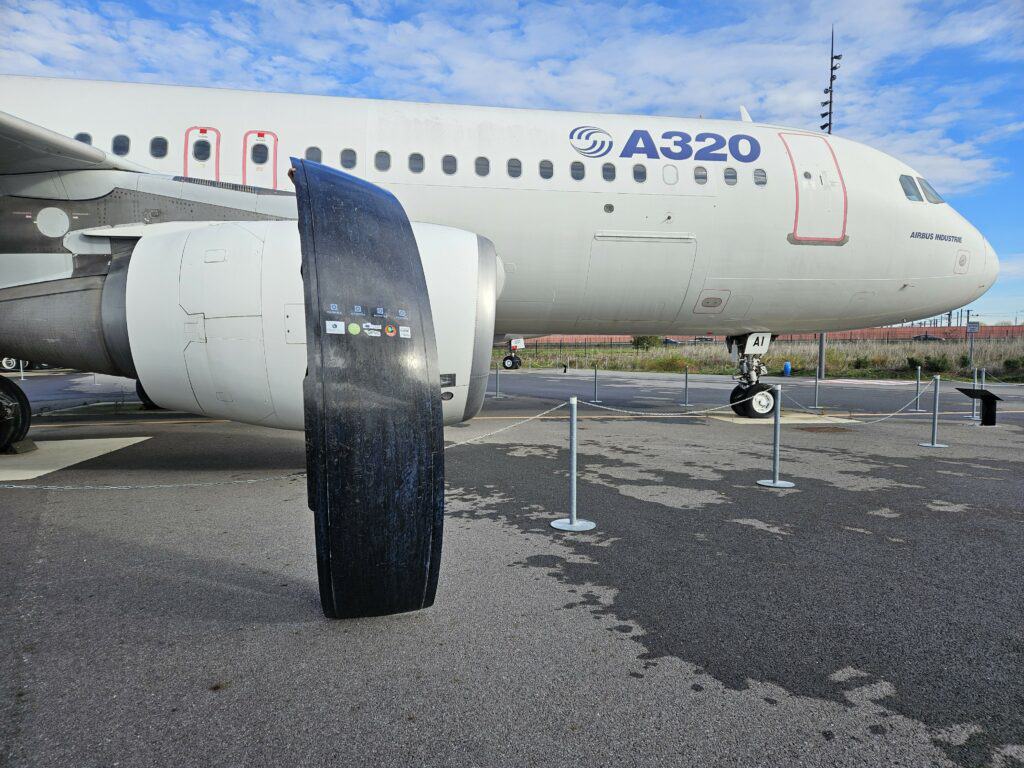
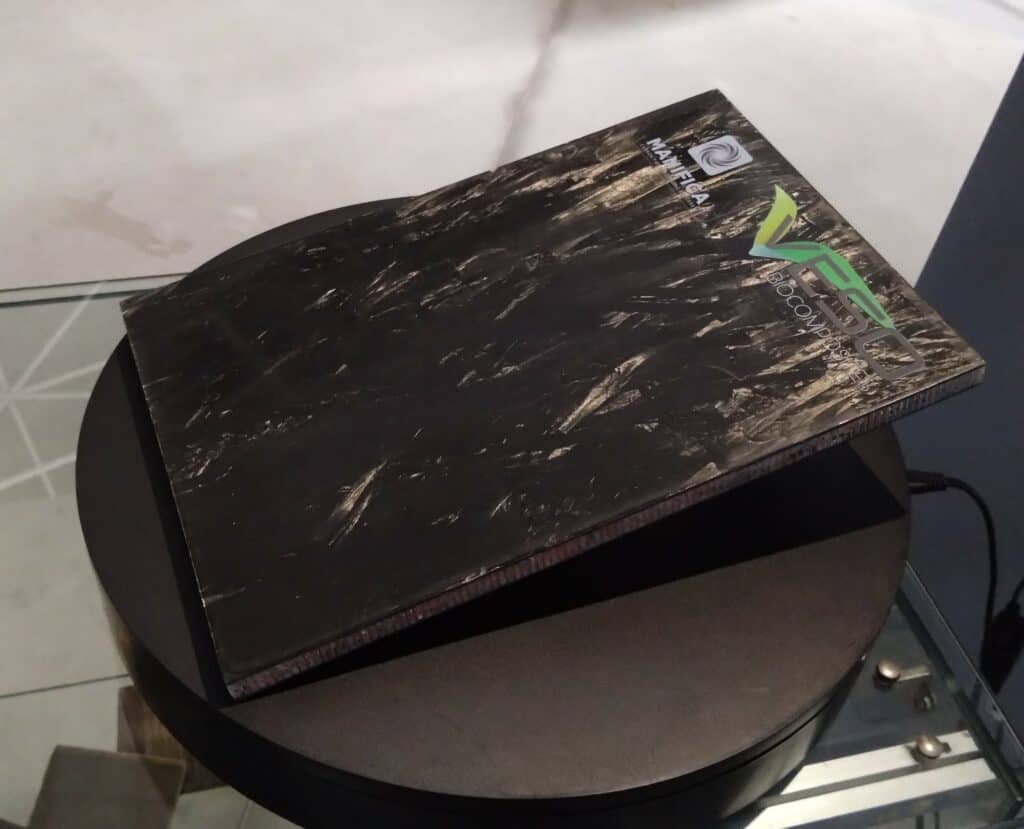
The manufacture of aeronautical parts paves the way for the use of rCF in many other applications: railway panels, boat floors, automotive frames, windmill blades…
Moreover, recycled carbon staple fibres provide new properties to rCF composite materials, such as vibration dampening or the opportunity to manufacture highly curved parts which is proof of the high added-value of the rCF developed by MANIFICA.
Project duration
39 months from July 2020 to September 2023
Project budget
€ 2 043 779 including € 1 743 119 EU funding
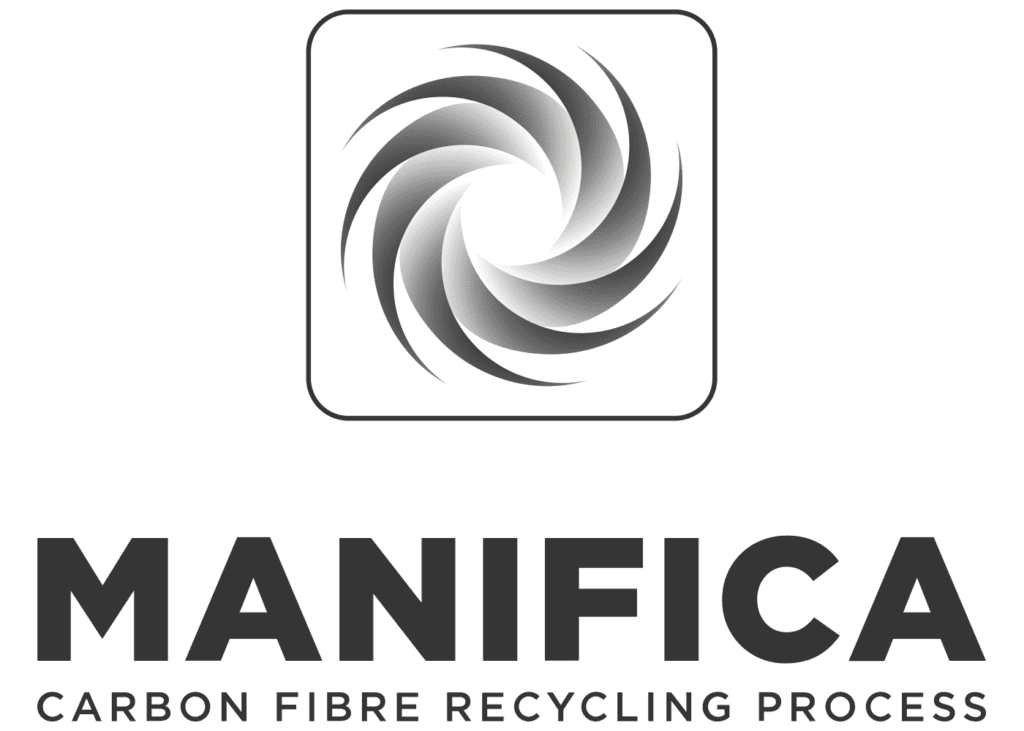
Partners of the project
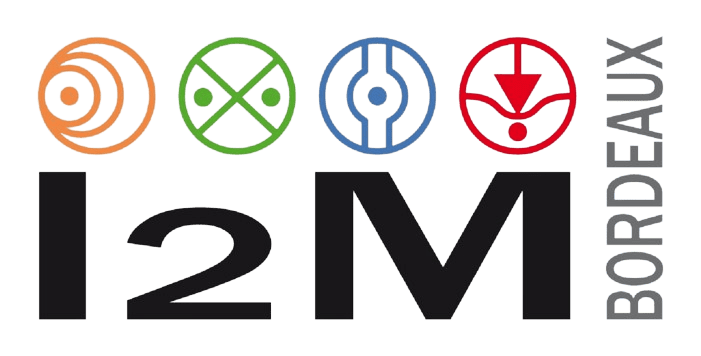
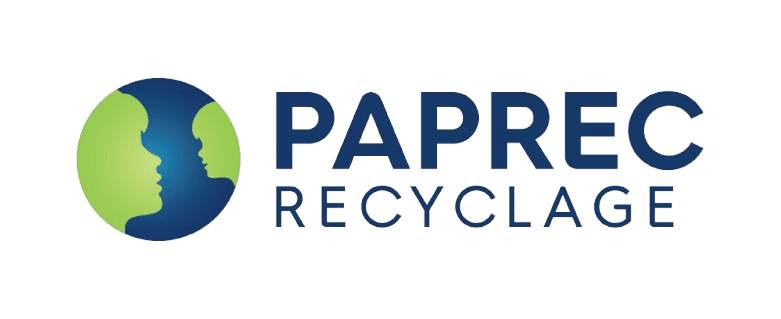
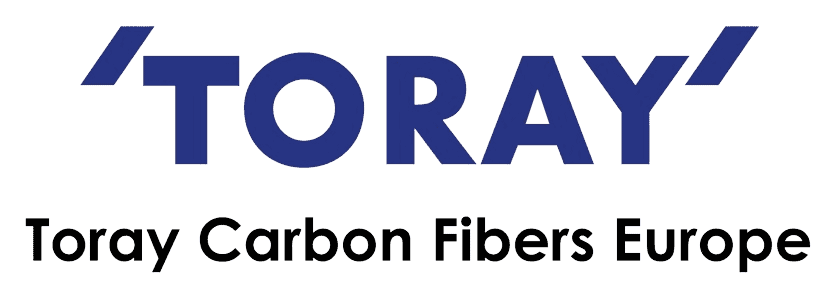
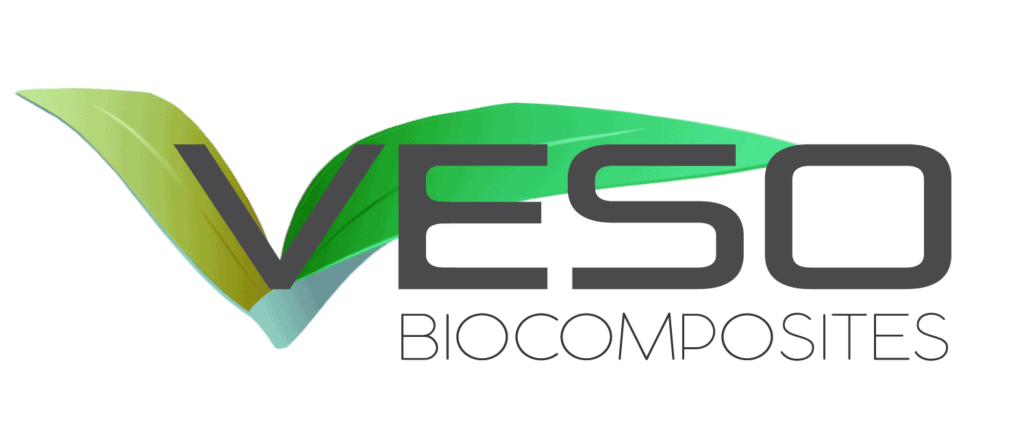
This project has received funding from the Clean Sky 2 Joint Undertaking (JU) under grant agreement No 887104. The JU receives support from the European Union’s Horizon 2020 research and innovation programme and the Clean Sky 2 JU members other than the Union.
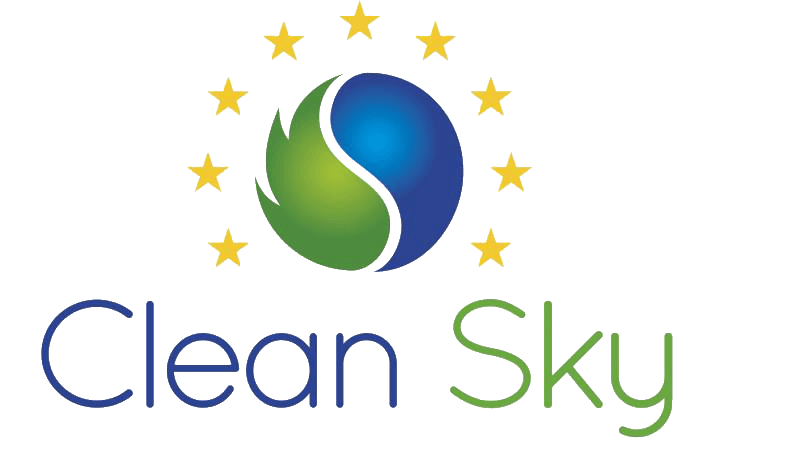
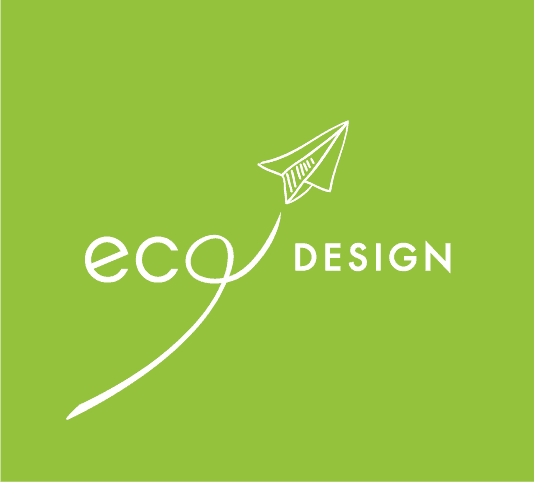
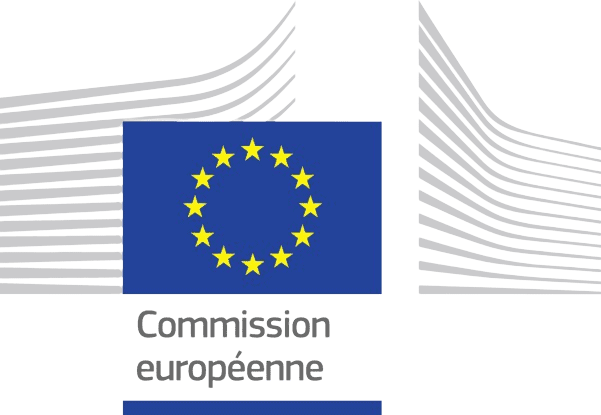